Exploring the Advantages of Silicone Injection Molding Machines in Electronics and Medical Supplies
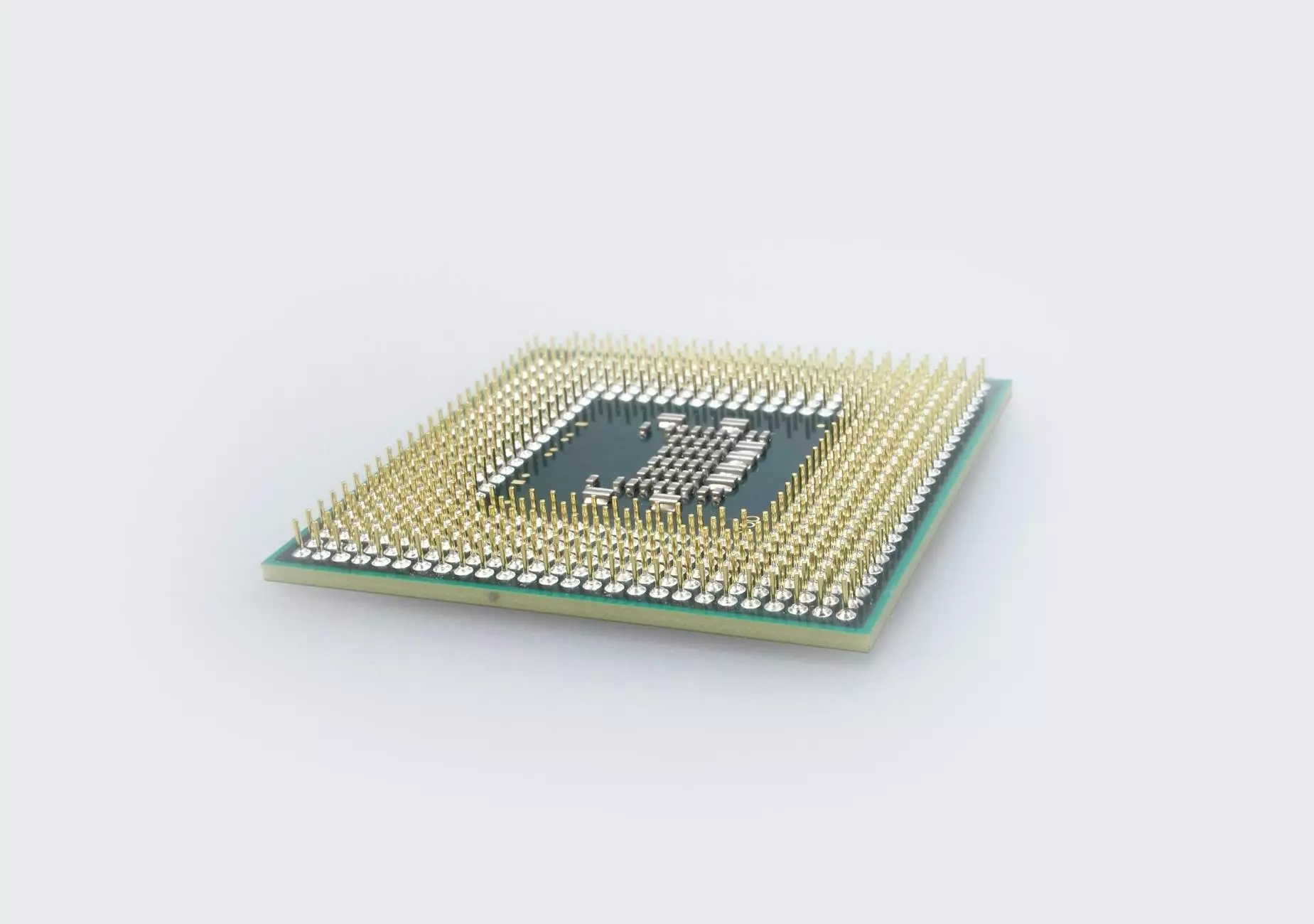
In the rapidly evolving world of manufacturing, silicone injection molding machines have emerged as a pivotal technology, particularly in the fields of electronics and medical supplies. Their efficiency, versatility, and ability to produce high-quality components make them invaluable tools for businesses aiming to enhance their production processes. This article delves into the intricacies of silicone injection molding machines, highlighting their applications, advantages, and the reasons why they are instrumental in driving innovation within these critical industries.
Understanding Silicone Injection Molding
Silicone injection molding is a manufacturing process that involves injecting liquid silicone rubber (LSR) into a mold to create various components. This method is highly effective for producing parts with intricate shapes and exceptional surface quality. With its increasing demand, businesses are investing significantly in silicone injection molding machines, recognizing their capacity to streamline production while ensuring high standards of quality and consistency.
The Role of Silicone Injection Molding Machines in Electronics
The electronics industry is characterized by rapid technological advancements and a relentless pursuit of miniaturization. Silicone injection molding machines play a crucial role in this sector by enabling the production of small, intricate components that are essential for modern electronics. Here are several ways in which they contribute:
1. Precision and Detail
The demand for precision in electronics manufacturing cannot be overstated. Silicone injection molding machines provide exceptional detail, ensuring that components fit together perfectly and function as intended. The ability to create complex geometries with intricate designs is a significant advantage for manufacturers in this field.
2. Enhanced Durability
Parts produced with silicone injection molding are known for their durability. Silicone rubber offers resistance to temperature extremes, UV radiation, and moisture, making it ideal for various electronic applications. This durability translates to longer-lasting products, reducing the need for frequent replacements and maintenance.
3. Lightweight Components
As electronics continue to evolve, the need for lightweight components becomes increasingly important. Silicone injection molding allows manufacturers to create lightweight parts without sacrificing strength or functionality. This feature is particularly beneficial for portable and wearable electronic devices.
Key Applications in Electronics
Several key applications in the electronics sector utilize silicone injection molding machines:
- Keypads and Switches: Silicone rubber is commonly used to create tactile keypads and switch covers, providing a user-friendly interface.
- Insulation Materials: Silicone's insulating properties make it ideal for components that require electrical insulation.
- Sealing Gaskets: Sealing applications benefit from silicone's flexibility and resistance to environmental factors.
The Importance of Silicone Injection Molding Machines in Medical Supplies
The medical industry demands the highest standards of cleanliness, precision, and reliability. Silicone injection molding machines meet these requirements exceptionally well, offering unique advantages to the production of medical supplies.
1. Biocompatibility
One of the foremost advantages of silicone rubber is its biocompatibility. This quality ensures that silicone products do not provoke adverse biological reactions, making them safe for use in medical applications. Silicone injection molding machines facilitate the production of items such as implants, seals, and tubing that can safely contact human tissue or fluids.
2. Cleanroom Manufacturing Capability
Many medical products must be manufactured in cleanroom environments to avoid contamination. Silicone injection molding machines can be adapted for cleanroom operations, ensuring that materials and production processes remain sterile and compliant with stringent medical regulations.
3. Customization and Scalability
The ability to customize products is critical in the medical field. With silicone injection molding, manufacturers can easily adjust mold designs and specifications to produce devices tailored to specific medical applications. This flexibility allows businesses to scale production up or down according to market demands.
Notable Applications in Medical Supplies
Silicone injection molding has numerous applications in the medical industry, enhancing the performance and safety of various products:
- Medical Tubing: Silicone tubing is employed for its flexibility and biocompatibility, ideal for various medical procedures.
- Drug Delivery Systems: Components in drug delivery systems are often made from silicone due to its ability to maintain structural integrity.
- Catheters and Implants: Silicone's biocompatibility makes it a preferred material for catheters and implants.
The Future of Silicone Injection Molding Machines
The future of silicone injection molding machines appears promising as advancements in technology continue to shape the landscape of manufacturing. Here are some anticipated trends that may impact their development and utilization:
1. Industry 4.0 Integration
The integration of Industry 4.0 technologies such as IoT, machine learning, and automation in silicone injection molding processes is set to revolutionize production efficiency. Smart machines that can monitor their operations and make adjustments in real-time will enhance output quality while minimizing wastage.
2. Sustainable Practices
As industries strive for sustainability, silicone injection molding processes will evolve to include environmentally friendly practices. This may involve the use of recycled materials and energy-efficient machinery, aligning with global sustainability goals.
3. Enhanced Material Development
The ongoing research in silicone materials will lead to the development of new formulations that offer improved properties such as enhanced strength, durability, and thermal resistance. These innovations will expand the potential applications of silicone in various sectors.
Conclusion
In summary, silicone injection molding machines are indispensable assets for businesses in the electronics and medical supplies sectors. Their ability to produce high-quality, durable, and precise parts at scale makes them ideal for meeting the demands of modern manufacturing. As technology continues to advance, the prospects for these machines and their contributions to various industries are limitless. For companies looking to enhance their production capabilities and product quality, investing in silicone injection molding machines is not just an option; it is a strategic necessity.
To explore more about how silicone injection molding machines can benefit your business in the electronics and medical supplies sectors, visit Nolato.com and discover a world of innovative solutions tailored to meet your manufacturing needs.